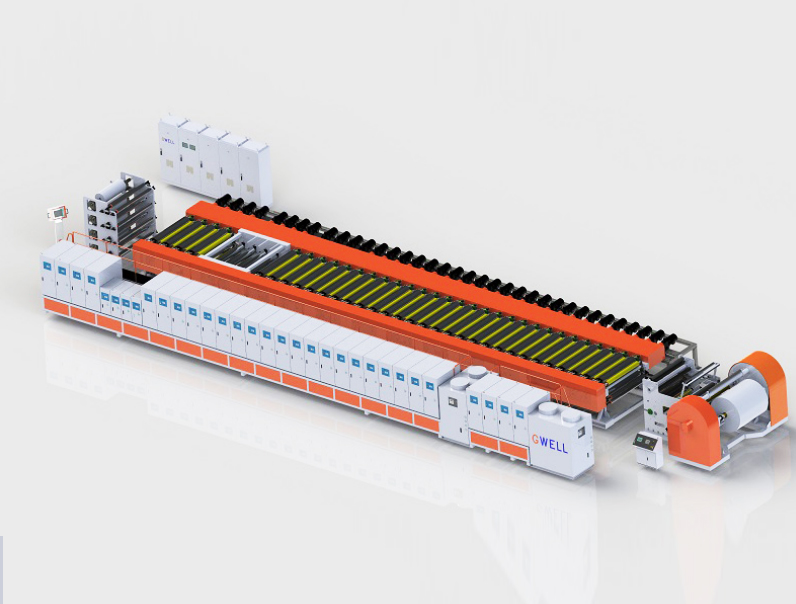
product details
(This figure is a schematic diagram of the dry single pull production line for power battery separators)
The main function of the longitudinal pull separator in lithium batteries is to separate the positive and negative poles of the battery, preventing short circuits caused by contact between the two poles. The micropores in the film can allow lithium ions to pass through, forming a charging and discharging circuit. The separator is a key material in lithium batteries and a high value-added material with high technical barriers. Its performance determines the interface structure, internal resistance, battery capacity, lifespan, and safety performance of the battery.
In the structure of lithium batteries, the separator is one of the key inner components. The performance of the separator determines the interface structure, internal resistance, and other characteristics of the battery, directly affecting its capacity, cycling, and safety performance. An excellent separator plays an important role in improving the overall performance of the battery. The colloquial description of the separator is a layer of porous plastic film, which is a high value-added material with the highest technical barrier among lithium battery materials, accounting for approximately 20% -30% of the cost of lithium batteries.
Jinwei Machinery specializes in manufacturing PP/PE lithium battery separator dry pull extrusion production lines, which can achieve stable and uniform stretching of products, uniform pores, and reduce defect rates.
(This figure is a schematic diagram of the lithium battery separator dry pull production line)
The lithium battery separator production line is divided into: dry unidirectional stretching production line; Dry bidirectional stretching production line; Wet extraction biaxial stretching production line.
Dry unidirectional stretching production line: The dry unidirectional stretching process is a method of producing hard elastic fibers, using PP or PE as the main raw material, mixing various grades of auxiliary materials, and thoroughly stirring to prepare low crystallinity high oriented polypropylene or polyethylene films. High crystallinity oriented films are then obtained through high-temperature annealing. This type of film is first stretched at low temperatures to form micro defects, and then pulled apart at high temperatures to form micropores. In terms of equipment, after extrusion molding by tape casting method, the multi-layer membrane is subjected to unidirectional stretching through a composite machine, and then the stretched multi-layer membrane is layered and cut by a layering machine and a slitting machine to produce a unidirectional stretched lithium battery membrane. The Jinwell lithium battery dry process single pull production line is equipped with high-precision testing instruments, mainly producing thicknesses of 16 μ M to 40 μ Different specifications of lithium-ion battery separators. Scope of application: large lithium-ion power batteries (electric vehicles, electric motorcycle, electric tools, large energy storage equipment, large military batteries)
Dry biaxial stretching production line: The dry biaxial stretching process uses PP as the main raw material and adds nucleating agents to polypropylene β Crystal form improver, which utilizes the density difference between different phases of polypropylene to undergo crystal form transformation and form micropores during stretching, is used to produce single-layer PP membrane battery isolation membranes. In terms of equipment, after extrusion molding by tape casting, bi-directional stretching and winding are then cut to produce bi-directional stretching lithium battery separators. Jinwei Lithium Battery Diaphragm Equipment is equipped with high-precision testing instruments, mainly producing thicknesses of 12 μ M to 40 μ Different specifications of double pull lithium-ion battery separators.
Wet biaxial stretching production line: The wet process uses PE as the main raw material to mix liquid hydrocarbons or some small molecule substances with polyolefin resin and stir them thoroughly. After heating and melting, a uniform mixture is formed, and then the temperature is lowered for phase separation to press the membrane. The membrane is then heated to a temperature close to the melting point, and biaxial stretching is carried out to orient the molecular chains. Finally, it is kept warm for a certain period of time, and residual solvents are washed off with volatile substances, It is possible to prepare interconnected microporous membrane materials. In terms of equipment, the wet bi-directional stretched lithium battery separator is produced by extrusion molding using tape casting method, followed by extraction process to form pores, and then vertical and horizontal stretching followed by winding and slitting. The Jinwell wet double pull lithium battery separator line is equipped with high-precision testing instruments, mainly producing a thickness of 8 μ M to 25 μ Different specifications of lithium-ion battery separators. Application scope: High performance lithium-ion batteries, etc.
(Diaphragm and electron microscope image of dry method single pull lithium battery)
Product features: The lithium-ion battery diaphragm is a kind of polymer functional material with nanometer micropores. Rechargeable lithium-ion batteries have the characteristics of high specific energy, long cycle life, no memory effect, and are safe, reliable, and can be quickly charged and discharged. It meets the great development needs of energy and environmental protection in various countries today, and its use in all walks of life is increasing rapidly.
1. Good uniformity of thickness and uniform distribution of micropores, which is conducive to the consistency of lithium-ion batteries;
2. Low porosity, good breathability, strong liquid retention ability, and low internal resistance of the battery;
3. High temperature resistance, no lateral thermal shrinkage, high film breaking temperature, and good safety performance;
4. High tensile strength and good mechanical properties;
5. The specifications of the production line are usually between 1000-2400mm in width, and the specific specifications are determined by the production process and can be customized.
Main applications of the products: power lithium-ion batteries for electric vehicles, electric motorcycle, electric bicycles, electric tools and other systems, large-scale energy storage lithium-ion batteries, and various digital lithium-ion batteries.
Lithium battery separator dry pull production line parameters (please consult sales engineer for details)
- Previous article:first a piece of writing
- Next article:Last article
Boutique Recommendation
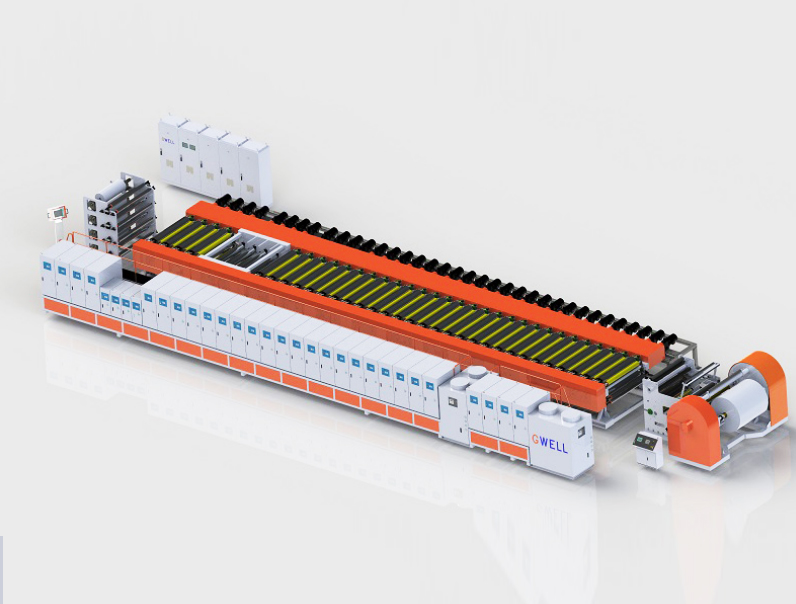